■はじめに
早いもので、「熱設計完全入門」を上梓してから二十余年の歳月が流れました。この間にエレクトロニクス製品は劇的に変わりました。薄型テレビ、スマホ、LED照明、EV、当時はなかったもので溢れています。
開発設計には熱流体シミュレーションが活用されるようになり、試作前の温度予測を可能にしました。それにもかかわらず依然として多くの製品で熱問題が発生しています。製品の小型・高性能化が進み限界設計を余儀なくされているのも事実ですが、本質的に何か足りないものがあります。それが、設計初期に行うべき「上流熱設計」です。
熱は感覚的に捉えることができる身近な現象なので、ある程度「勘と経験」が生かせます。しかし、伝熱のメカニズムは複雑で定量把握が困難なため、数値化はシミュレーションに頼ります。その結果、「勘と経験で設計して、シミュレーションで修正する」という設計パターンができ上がります。
このパターンではシミュレーションは実験代替えなので精度が求められます。しかし精度を追求するほど「予測コスト」が膨らみます。また予測が正確であってもそれが「適切な熱設計」につながるとは限りません。
短期間での高度な製品設計が要求される現在、"温度を確認して対処する"いわば「後出し(・・・)熱設計」は限界に来ています。"熱的要件から冷却機能を創り上げていく"、「上流熱設計」こそが、こうした状況から脱却する唯一の手段なのです。
本書ではこの「上流熱設計の実践」のために必要な知識、ツール、手法、手段、プロセスについて、誌面の許す限り詳しく解説しました。そうした意気込みを「完全制覇」というタイトルに込めています。
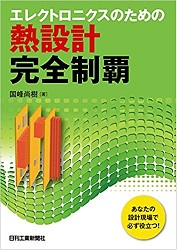
■構成
本書は熱設計プロセス構築に至るまでを下記のステップで構成しています。
◆熱設計の基礎
第1章、2章、3章では、熱設計の基本的事項と放熱のメカニズム、熱設計で使用する計算式について解説しました。
◆予測ツールと計測ツール
第4章、第5章では、熱設計に欠かせない温度予測ツールと熱計測方法、および部品温度管理の考え方について説明してあります。
◆熱設計手法
第6章、7章、8章では、機器や基板、コンポーネントの熱設計で使う手法や常套手段について解説しています。
◆冷却デバイス
第9章、10章、11章では、放熱材料や冷却デバイスについて、その使用方法や注意点、液冷システムの設計方法などについて詳述しました。
◆熱設計プロセス
第12章では、3つの熱設計事例をもとに熱設計のプロセスを解説しています。
実製品の事例を掲載できないため、仮想製品モデルを対象としていますが、考え方や手法を理解していただければ幸いです。
熱設計の実施にあたって必要なExcel計算シートも準備しました。
■A5判並製348頁 ■定価(本体3,456円税込) ■国峰尚樹 編著 ■日刊工業新聞社社 発行(2018年5月28日)
■目次
第1 章 製品開発のキー技術となった「熱設計」
〜部品の小型化と製品の多様化が熱設計を変えた〜
1.1 熱対策から熱解析、そして熱設計へ 1
1.2 実装技術の進展と冷却技術の変遷 2
1.2.1 「発熱集中」が少ない時代の冷却方式
2
1.2.2 発熱集中が冷却方式を多様化した3
1.3 部品の小型化がもたらしたインパクト 5
1.4 「発熱量の見積」が熱設計の要 6
1.4.1 そもそもなぜ熱がでるのでしょう
6
1.4.2 どれくらいが熱になるのか?
7
1.4.3 出力100W
のアンプは発熱量100W か? 9
1.4.4 発熱量の予測と計測
10
1.5 熱による不具合も様変わり 13
1.5.1 熱で機器が動かない! 熱暴走の危険
13
1.5.2 熱で機能が制限される 〜長く動かせれば商品の差別化に〜
14
1.5.3 低温やけどでクレーム!
14
1.5.4 さまざまな原因で部品は壊れる
16
第2 章 伝熱のメカニズムと放熱促進
〜熱をミクロに捉えてその振る舞いを知っておこう〜
18
2.1 熱はどのように発生し伝わっていくのか?
18
2.2 部品の中は熱伝導で伝わる 20
2.2.1 電気を伝えやすい材料は熱も伝えやすい
20
2.2.2 熱伝導率は測定方法で異なる
21
2.3 表面からは空気の熱伝導と移動の複合現象「対流」で放熱
23
2.3.1 対流促進には「温度境界層」を薄くする
23
2.3.2 流速を上げると温度境界層は薄くなり、やがて乱れる
26
2.3.3 内部に空間のある密閉筺体 〜対流と熱伝導は紙一重!〜
27
2.3.4 伝熱工学とCFD
の違いは「熱伝達率」 28
2.4 熱放射によって物体間で直接熱交換する
29
2.4.1 温度が高くなると放射される電磁波は強く、波長が短くなる
32
2.4.2 色と放射率は直接関係しない
33
2.4.3 単色放射率と単色吸収率は同じ
34
2.5 通風口による換気 35
2.5.1 ファンや通風口で筐体の換気風量を制御する
35
2.5.2 風量が決まるメカニズム
36
2.6 熱源を筺体に接触させて熱を逃がす
37
2.7 温まりにくいものを使って温度上昇を抑える
38
2.8 熱対策における伝導・対流・放射の役割とは
39
2.8.1 熱伝導では温度の均一化しかできない
39
2.8.2 平均温度を下げるのは対流か熱放射
40
第3 章 熱設計に使用する計算式
〜熱をマクロにとらえて放熱に効くパラメータを押さえよう〜
41
3.1 伝熱を支配する基礎方程式 31
3.2 熱移動を1
つの式で表現する 〜熱のオームの法則〜 42
3.3 放熱のイメージと言葉を理解しましょう
44
3.3.1 温度(水位)、熱量(水量)、熱流量(注水量)
44
3.3.2 熱抵抗(管路抵抗)、熱容量(底面積)
45
3.4 熱伝導の計算で使用する代表的な式 48
3.4.1 熱伝導形状係数 48
3.4.2 等価熱伝導率 50
3.4.3 接触熱抵抗の計算 54
3.4.4 拡がり・狭まりの熱抵抗
55
3.5 対流の計算で使用する式 56
3..5.1 伝熱工学で登場する無次元数
57
3.5.2 空気中の物体の自然対流平均熱伝達率
59
3.5.3 空気中の物体の強制対流平均熱伝達率
61
3.5.4 管内の熱伝達率 63
3.5.5 高高度や低圧下での熱伝達率
64
3.6 熱放射の基礎式と電子機器向けの式への変換
65
3.6.1 単体の熱放射の基礎式
65
3.6.2 2 面間の熱放射の式 66
3.6.3 電子機器向けの放射計算式
67
3.6.4 COS4 乗則 68
3.7 筐体熱設計に不可欠な「物質移動による熱輸送の式」
69
3.7.1 物が動けば熱も移動する
69
3.7.2 必要な換気風量や通風口面積を求める
71
3.8 通風抵抗とファン動作点の計算式 72
3.8.1 流れのオームの法則
73
3.8.2 圧損係数と通風抵抗
73
3.8.3 圧損係数の計算 75
3.8.4 流体抵抗の合成 77
第4 章 熱設計の手法とツール
〜熱設計は徹頭徹尾「熱抵抗」で考える〜
79
4.1 伝熱基礎式を製品の熱計算に適用するには
79
4.1.1 電子機器用の簡易計算式の利用
79
4.1.2 図表・グラフの活用
80
4.1.3 Excel による伝熱計算
82
4.1.4 Excel
による熱回路網法計算 83
4.2 伝熱基礎式を冷却機構の設計に適用するには
85
4.2.1 「熱抵抗」を中心に考える 〜なぜ熱抵抗を使うか〜
87
4.2.2 「目標熱抵抗」と「対策熱抵抗」を対比して考える
90
4.3 骨太の熱抵抗で放熱経路を構造化する 〜まず木を見ず森を見る〜
92
4.3.1 熱抵抗モデルで機器の放熱ルートを決める
94
4.3.2 熱抵抗に含まれるパラメータから熱対策をリストアップする
95
4.4 強力な助っ人、熱流体解析ソフトウエア(CFD)を活用しよう
96
4.4.1 CFD
活用のメリットと注意点 98
4.4.2 解析精度を追求する前に個人差をなくす努力を
98
4.4.3 解析精度の目標 100
4.4.4 温度予測ツールの使い分け
101
第5 章 温度管理と熱計測
〜
適切な温度管理と精度のよい測定で機器の信頼性を確保しよう〜
102
5.1 部品の温度測定と温度管理 102
5.1.1 「部品温度」の定義
102
5.1.2 半導体部品で定義される熱抵抗・熱パラメータ
103
5.1.3 ジャンクション温度の推定
104
5.1.4 端子部温度規定
5.1.5 周囲温度のみで規定される部品への対応
109
5.2 熱電対による温度測定 110
5.2.1 熱電対による温度測定誤差の原因
110
5.2.2 温度測定誤差の例 113
5.2.3 その他の測定誤差にも注意
115
5.3 サーモグラフィーによる温度測定 116
5.3.1 測定精度を決める放射率設定
117
5.3.2 サーモグラフィーの解像度
118
5.4 抵抗法による巻線の温度測定 119
5.5 半導体のジャンクション温度測定 120
5.6 熱抵抗の測定 122
5.6.1 ASTM D5470(接触熱抵抗・熱伝導率測定)
122
5.6.2 T3Ster(過渡熱抵抗測定)
123
5.7 熱流量・熱流束の測定 126
5.8 風量や圧力・通風抵抗の測定 128
第6
章 自然空冷機器の熱設計の常套手段
〜戦わずして逃げ道へ誘導せよ〜
131
6.1 自然換気を使って放熱する機器 131
6.1.1 どれくらいの通風換気が必要か? 自然空冷で大丈夫か?
131
6.1.2 排気口と吸気口の見分け方 〜発熱中心〜
132
6.1.3 発熱中心を下にして煙突効果を得る
137
6.1.4 大切なのは吸気口よりも排気口!
138
6.1.5 「最も狭い部分」を通風口面積と考える
139
6.1.6 通風口のスリットは細くしすぎない
140
6.1.7 排気口はできるだけ高い位置に設ける! 吸気口の配置は自由
141
6.1.8 自然空冷機器は狭い空間を作ってはいけない
142
6.2 内部空間のある密閉機器の設計 144
6.2.1 通風口の放熱能力と筐体表面の放熱能力の比較
144
6.2.2 密閉筐体の放熱 〜内部に空間が空いている場合〜
145
6.2.3 アルミの筐体より樹脂の筐体の方が冷える!?
148
6.3 内部に空間がない密閉筐体の設計 150
6.3.1 密閉機器では「熱伝導のリレー」で熱を運ぶ
150
6.3.2 骨太の放熱経路設計
152
6.3.3 接触熱抵抗低減 〜TIM
の活用〜 153
6.3.4 ヒートスプレッダー
154
6.3.5 高放射材料
6.4 屋外で使用する機器 156
6.4.1 日射による受熱量の大きさ
156
6.4.2 日射が機器に及ぼす影響
156
6.4.3 日射対策 159
6.4.4 防寒と結露 161
第7 章 強制空冷機器の熱設計
〜空気を集めて熱を一掃せよ〜
163
7.1 冷却ファンの振る舞いを知っておこう 163
7.1.1 換気扇と扇風機 〜冷却ファンの役割と特性の違い〜
163
7.1.2 ファンの基本特性と通風抵抗
165
7.1.3 知っておくと便利なファンの相似則
166
7.1.4 ファンの並列・直列運転・回転数増加
167
7.1.5 ファン騒音の相似則
169
7.1.6 ファンは最大出力点で使うと静かに動く
169
7.1.7 素直な流れの吸気側、癖のある流れの排気側
171
7.1.8 ファン近傍の障害物の影響
174
7.2 強制空冷機器の熱設計のポイント 176
7.2.1 強制空冷と自然空冷の違い
176
7.2.2 強制空冷機器ではバイパスの防止が重要
176
7.2.3 強制空冷では通風口を開けすぎない
177
7.2.4 ファンの開口面積よりも狭い場所を作らない
179
7.2.5 ファンの取り付けはPULL
型かPUSH 型か? 180
7.2.6 PULL
型は通風口が狭いと予想外の場所から吸い込んでしまう!
182
7.2.7 PUSH
型の乱流効果を活用する 182
7.2.8 ファンを使った部品冷却の常套手段
184
7.2.9 流路パターンとその注意点
185
7.3 強制空冷機器の設計手順 188
7.3.1 換気風量を決めてファンを選ぶ(換気量設計)
188
7.3.2 ファン動作風量を推定する
189
7.3.3 発熱体周囲の風速を確認する
190
7.4 吹付ファンによる冷却(モータ冷却の例)
191
7.4.1 吹付ファンで得られる風速
191
7.4.2 ファンで強制空冷された発熱体の温度上昇計算
192
7.4.3 ファンの大きさや発熱体との距離の影響
193
7.5 防塵対策 194
7.5.1 フィルターの負荷は大きい! 取り込み口を大きく
195
7.5.2 フィルターは吸気口に密着させてはいけない
195
7.5.3 フィンやスリットの間口を広くする
第8
章 部品と基板の熱設計 熱源分散と熱拡散に努めよ
〜全体を骨太に設計し部品ごとに対策を仕分ける〜
197
8.1 半導体デバイスやモジュールの熱対策 197
8.1.1 部品の熱対策は「均熱化」と「外部接続強化」
197
8.1.2 高発熱デバイスは内部熱抵抗の低減が課題
199
8.2 基板の熱設計に必要な2 つのアプローチ@ 〜基板を俯瞰した熱設計〜
201
8.2.1 平均熱流束を計算する
201
8.2.2 局所熱流束を計算する
202
8.2.3 「熱源集中」が不可避であれば「熱拡散」を図る
202
8.2.4 高熱伝導基板は「熱流束」の管理が大切
205
8.2.5 低熱伝導基板は部品レイアウト(風上・風下)が大切
207
8.3 基板の熱設計に必要な2 つのアプローチA 〜部品視点の熱設計〜
207
8.3.1 目標熱抵抗と単体熱抵抗 〜自己冷却可能か不能か〜
208
8.3.2 「基板で冷やせる部品」と「基板では冷やせない部品」
210
8.4 高放熱基板 212
8.4.1 基板の放熱能力の測定と評価(JPCA
規格) 212
8.4.2 放熱能力の高い基板
215
8.5 筐体への放熱 216
8.5.1 基板放熱限界を超えたら熱は筐体に逃がす
217
8.5.2 筐体放熱効果の計算(熱回路網法)
218
8.6 配線パターンやケーブルのジュール発熱
222
8.6.1 ジュール発熱による温度上昇の予測
223
8.6.2 表皮効果 224
8.7 通風を考慮した基板のレイアウトを行う
225
8.7.1 基板を水平に重ねて置かないようにする
225
8.7.2 複数の基板を垂直に配列する際には最適ピッチで配置する
226
8.7.3 高発熱基板どうしはできるだけ隣接させない
228
8.7.4 基板を上下に配置する場合には遮蔽板を設ける
228
8.7.5 強制空冷ではバイパスをカットする
228
第9 章 放熱材料の使い方
〜放熱経路構築の具を利用せよ〜
230
9.1 TIM(Thermal Interface Material) 230
9.1.1 サーマルグリースの種類と選定法
231
9.1.2 熱伝導シートの種類と選定法
235
9.1.3 PCM(Phase Change Material)
240
9.1.4 ゲル(熱伝導性液状充填材)
241
9.1.5 その他の放熱材料 241
9.2 ヒートスプレッダ 242
9.2.1 シールド材やフレーム板金を使ったヒートスプレッダ
242
9.2.2 グラファイトシート(黒鉛シート)
244
9.2.3 金属箔を使ったヒートスプレッダ、高放射シート
244
9.2.4 ヒートスプレッダの性能概算
245
9..3 断熱材と蓄熱材 245
9.3.1 断熱材 245
9.3.2 真空断熱材とシリカエアロゲル
246
9.3.3 蓄熱材 246
第10 章 ヒートシンク活用術
〜吸収拡散の具を駆使せよ〜
248
10.1 ヒートシンクの種類 248
10.2 ヒートシンクには3 つの熱抵抗がある 249
10.3 ヒートシンクベース面の「拡がり熱抵抗」の計算
250
10.4 自然空冷ヒートシンクの選定・設計の手順
252
10.5 知っておくべきヒートシンクの常識 257
10.5.1 自然空冷ヒートシンクの熱抵抗は温度で変わる
257
10.5.2 包絡体積が同じでも熱抵抗は異なる
258
10.5.3 熱源の大きさや配置で熱抵抗は変わる
259
10.5.4 ヒートシンクベースの「厚み」はホットスポットを解消し温度変動を抑える
259
10.5.5 ヒートシンクの性能評価は「ヒートシンク温度」を基準にしてはいけない
260
10.5.6 ヒートシンクメーカの熱抵抗測定方法は製品で異なる
260
10.5.7 プレート型ヒートシンクは指向性が大きい
260
10.5.8 フィン高さが増すほど熱放射の割合が減る
261
10.5.9 アルマイトや塗装色に大きな差はない
261
10.5.10 フィン表面の微細加工は自然空冷では効果がない
263
10.5.11 かしめヒートシンクは製造ばらつきがある
263
10.5.12 自然空冷ヒートシンクでは近くに流れを妨げるものを置かない
263
10.6 強制空冷ヒートシンクの選定・設計の手順
264
10.7 強制空冷ヒートシンク設計における留意点
269
10.8 ヒートシンクの過渡熱応答 271
第11 章 ヒートパイプ・電子冷却・液冷
〜飛び道具を活用せよ!〜
274
11.1 ヒートパイプ 274
11.1.1 動作メカニズムと性能
275
11.1.2 ヒートパイプの種類
275
11.1.3 ヒートパイプの用途
277
11.1.4 注意点@ 最大熱輸送量
278
11.1.5 注意点A トップヒートモード
278
11.1.6 注意点B 取り付け(接触熱抵抗)
279
11.1.7 注意点C 曲げ加工
279
11.1.8 プレイステーション3
での活用例 280
11.2 液冷システムの設計 281
11.2.1 液冷システムの構成
281
11.2.2 液冷システムの計算の流れ
283
11.2.3 液冷システムの計算例
284
11.2.4 冷媒の選定 291
11.3 ペルチェモジュール(熱電素子:TEC)
291
11.3.1 動作メカニズムと予測式
291
11.3.2 ペルチェモジュールを使った計算例
293
11.3.3 ペルチェモジュール使用上の注意点
295
第12
章 製品設計に見る熱設計のプロセス
〜熱設計は手順を踏んで効率的に進めましょう〜
297
12.1 基本的な熱設計手順 297
12.2 【事例1】密閉機器の熱設計 299
12.3 【事例2】自然空冷通風機器の熱設計 307
12.4 【事例3】強制空冷機器の熱設計 318
12.5 まとめ 330
文献・使用ソフト
索引
戻る
|